
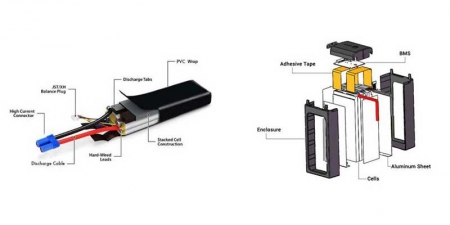
The present work investigates the scenario of the battery industry in order to implement a blockchain-based platform for the supply chain implementation thus allowing a better control on performance of batteries and environmental impact. A large number of parameters have a role on battery's health and thousands of data need to be evaluated and combined. Life expectancy is affected on manufacture, but also on operational conditions. The growing adoption of electric vehicles on the market has increased the demand for batteries that may have numerous manufacturers. The use of technologies such as Internet of Things (IoT), data processing and blockchain have allowed companies to serve their customers with better quality, efficiency, reliability and in the shortest possible time. Finally, future LCAs must transition away from kg of battery mass as a functional unit and instead make use of kWh of storage capacity and kWh of lifetime energy throughput. Third, LCAs should explore at least 2–3 battery manufacturing facility scales to capture size- and throughput-dependent impacts such as dry room conditioning and solvent recovery. Second, future studies should account for extraction and processing operations that deviate from industry best-practices and may be responsible for an outsized share of sector-wide impacts, such as artisanal cobalt mining. First, LCAs should focus analyses of resource depletion on long-term trends toward more energy and resource-intensive material extraction and processing rather than treating known reserves as a fixed quantity being depleted.

This review explores common practices in lithium-ion battery LCAs and makes recommendations for how future studies can be more interpretable, representative, and impactful. Nonetheless, life cycle assessment (LCA) is a powerful tool to inform the development of better-performing batteries with reduced environmental burden. Rechargeable batteries are necessary for the decarbonization of the energy systems, but life-cycle environmental impact assessments have not achieved consensus on the environmental impacts of producing these batteries. The outcomes of this work can support policy designers and battery industry leaders in managing production technology and location. Finally, a comprehensive sensitivity analysis is conducted to investigate the final prices of battery cell chemistries due to the changes in commodities prices, economic factors of the plant, battery cell production parameters, and production volume. This difference could decrease by approximately 31% at the minimum efficient scale of the battery production plant, which is 7.8 GWh.year −1 for the case study in this work. For a case study plant of 5.3 GWh.year −1 that produces prismatic NMC111-G battery cells, location can alter the total cost of battery cell production by approximately 47 US$/kWh, which is dominated by the labor cost. In this regard, a process-based cost model (PBCM) is developed to investigate the final cost for producing ten state-of-the-art battery cell chemistries on large scales in nine locations. Moreover, such a model is helpful in finding the minimum efficient scale for the battery production plant which complies with the emergence of Giga-battery plants. Thus, developing a cost model that simultaneously includes the physical and chemical characteristics of battery cells, commodities prices, process parameters, and economic aspects of a battery production plant is essential in identifying the cost-intensive areas of battery production. Further, obtaining a high-quality battery at the end of the production line requires integrating numerous complex processes. On the other side, despite the increase in the battery cell raw material prices, the total production cost of battery cells requires reaching a specific value to grow cost-competitive with internal combustion vehicles. In response to the increasing expansion of the electric vehicles (EVs) market and demand, billions of dollars are invested into the battery industry to increase the number and production volume of battery cell manufacturing plants across the world, evident in Giga-battery factories.
